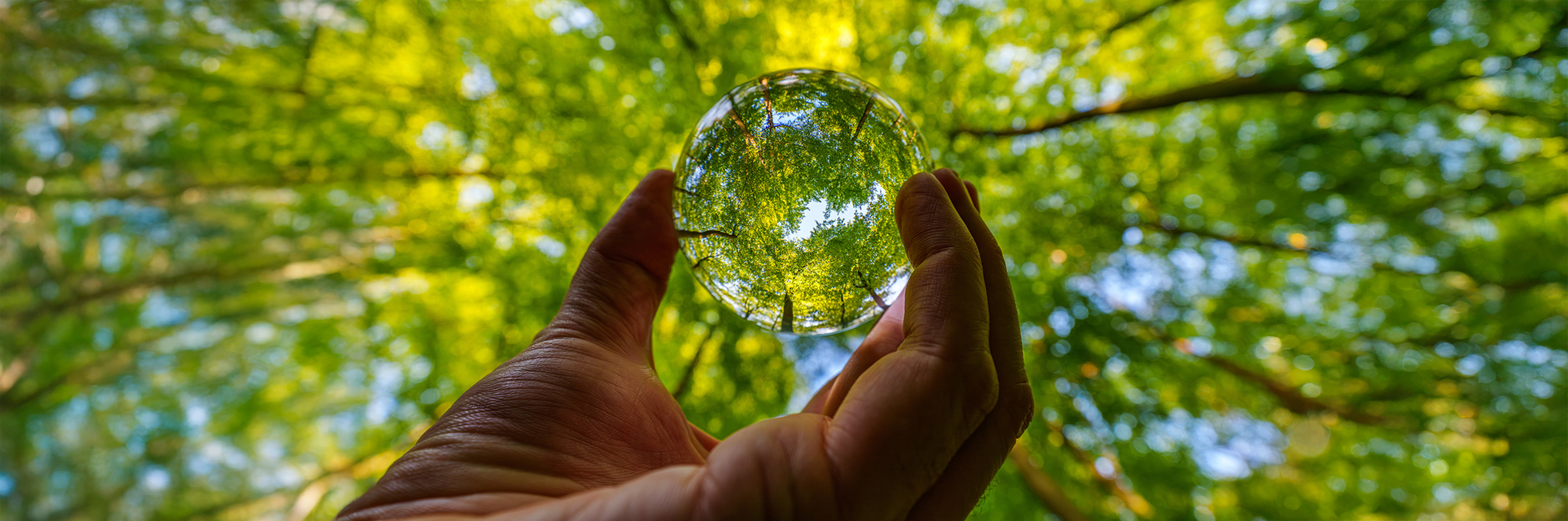
Sustainable ScanBox
Sustainability at ScanBox
At ScanBox, sustainability is a natural and integrated part of our business. Our products and solutions are designed to support more sustainable food logistics by creating efficient and optimized workflows that reduce food waste and energy consumption.
Over the past decades, the Earth's resources have been put under greater pressure than ever before, with a rapidly growing population and increasing demands for food and energy. In these challenging circumstances, ScanBox has a vital commitment: to actively reduce our climate footprint, improve working conditions in our industry and contribute to a more equitable and balanced world.
We view sustainable development as using the Earth's resources responsibly to meet today's needs without compromising the ability of future generations to meet theirs. This is an ongoing journey, and we are determined to continue learning and improving along the way.
Learn more about how we work with sustainability in our Sustainability Policy.
Let’s strive toward a more sustainable world together!
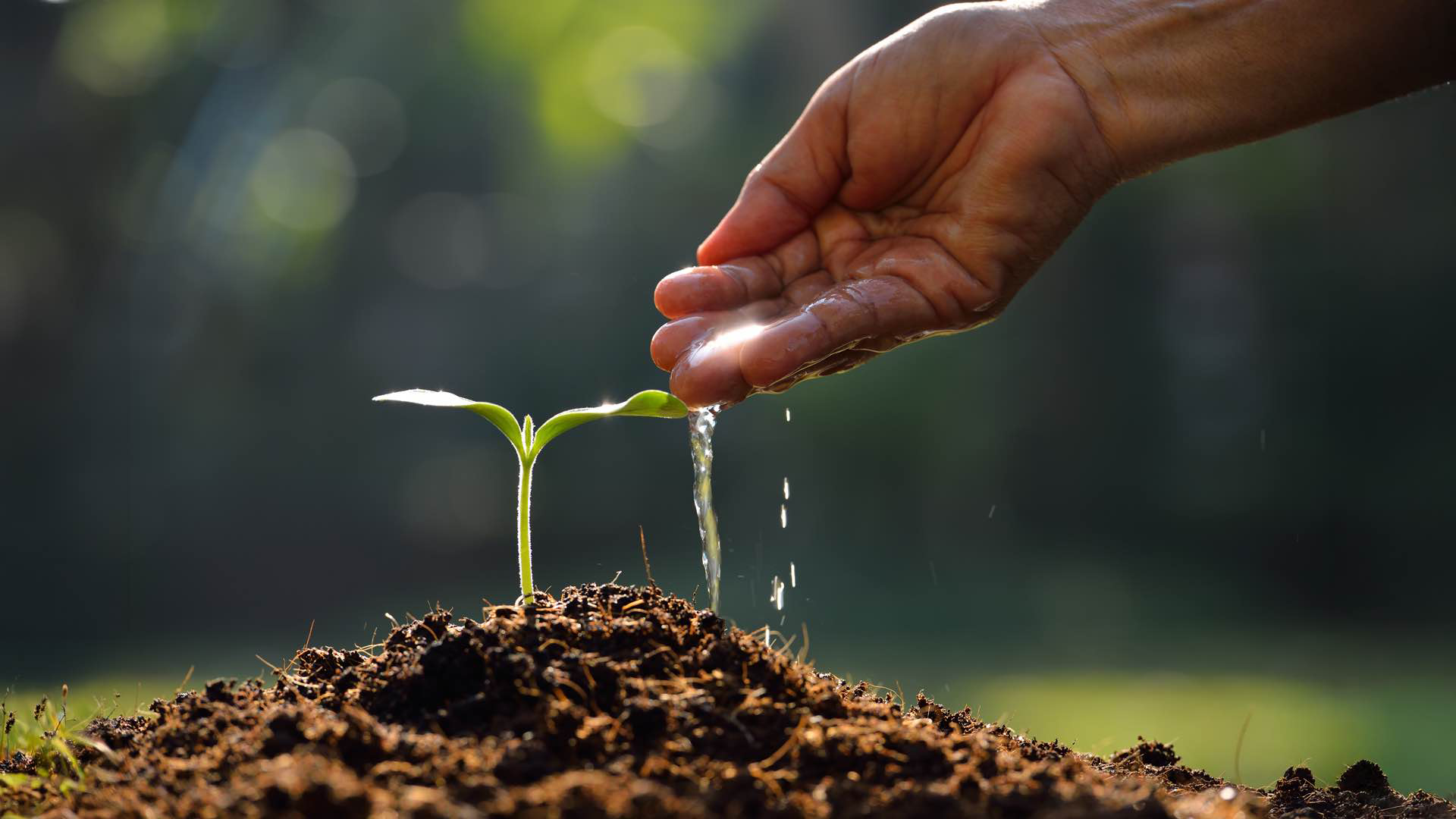
How we manage our climate impact
The Greenhouse Gas Protocol (GHG Protocol) is the world’s most widely used standard for measuring and reporting greenhouse gas emissions. The protocol divides emissions into three categories:
- Scope 1 includes direct emissions from sources owned or controlled by us, such as factories and vehicles.
- Scope 2 encompasses indirect emissions from purchased energy, such as electricity and heating.
- Scope 3 includes other indirect emissions across the value chain, such as materials from suppliers, inbound and outbound transport, and waste management.
Minimal climate impact from our direct emissions
Looking at Scope 1 category, we have never depended on fossil fuels for heating or engaged in chemical processes that contribute to climate change during production. Our electric forklifts and electric & hybrid vehicle policies minimize our direct emissions.
-
No fossil fuels or chemical processes in the factory
-
Electric forklifts only
-
Electric and hybrid vehicle policy for all company cars
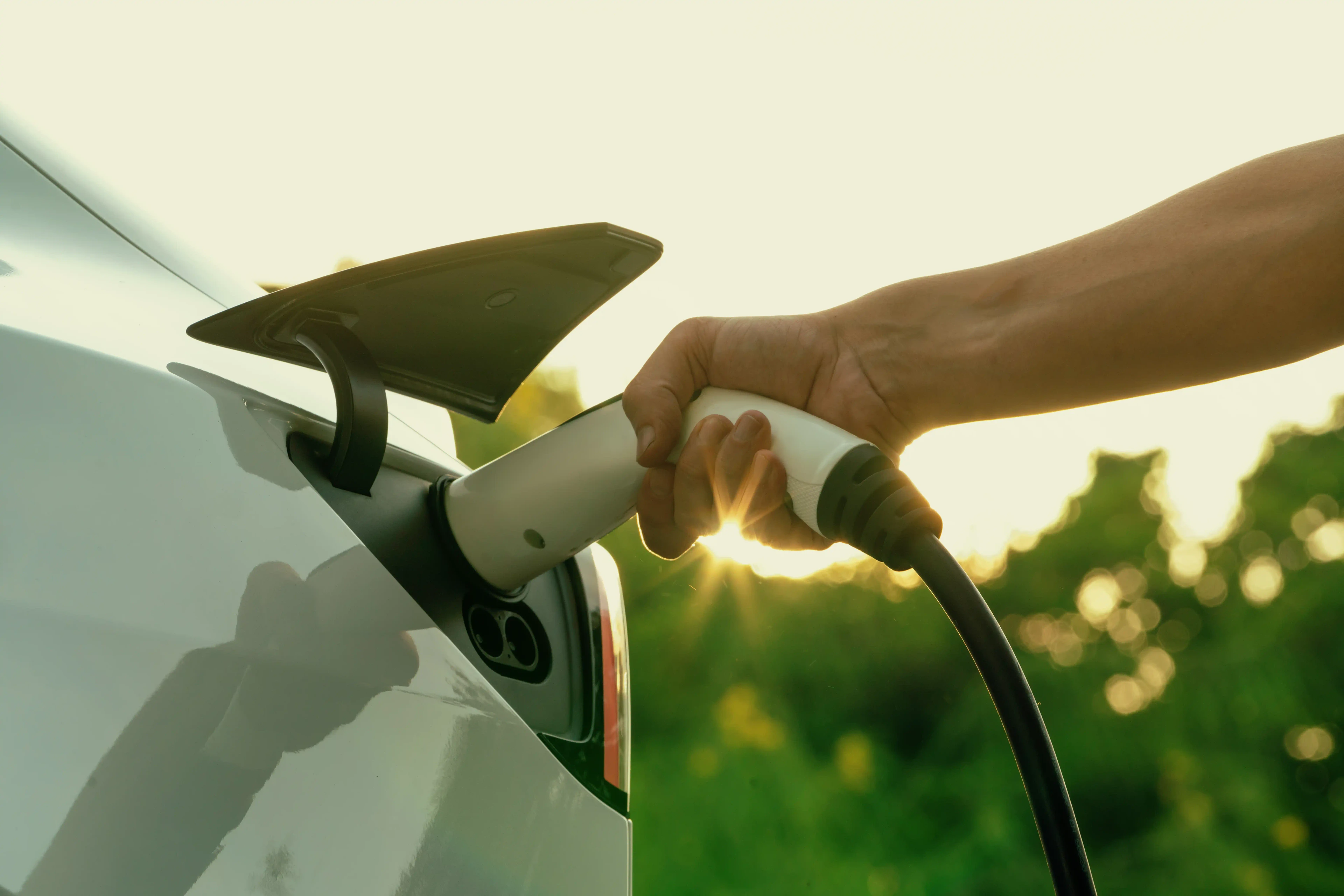
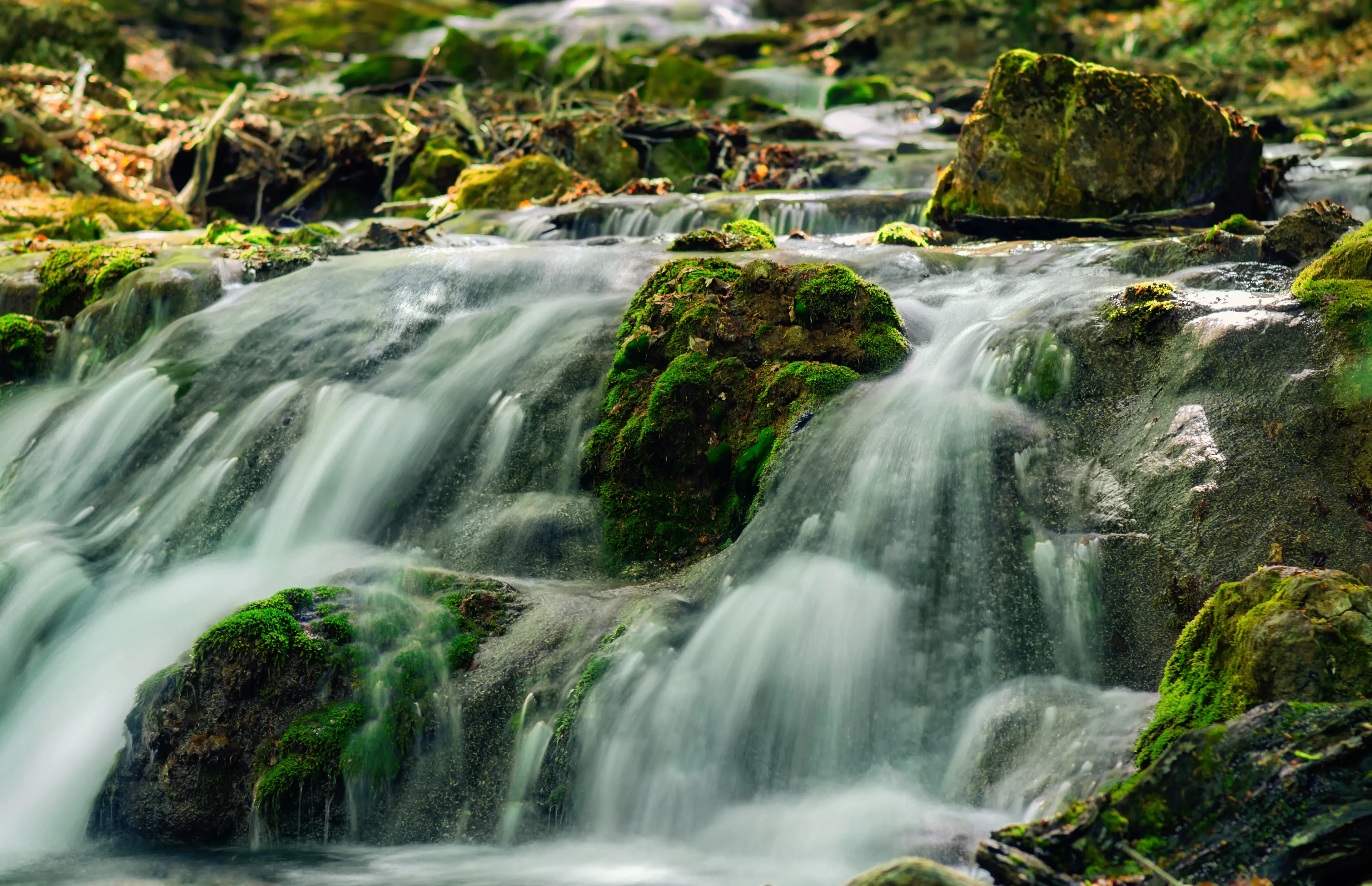
85% lower climate impact per unit
Regarding Scope 2 category, we have reduced our climate impact from purchased energy by over 85% through investments in green energy and energy efficiency. These efforts are integral to reducing our carbon footprint and achieving our sustainability goals.
-
New and more efficient ventilation systems
-
Installed low-energy lighting and motion sensors
-
Energy supply primarily from renewable hydropower
Focusing on indirect emissions
Scope 3 is the most extensive and complex category of emissions reporting as it covers all indirect emissions throughout the value chain. To effectively reduce these emissions, we have initiated thorough mapping and taken concrete measures to reduce our climate footprint:
-
Reduced waste and 100% recycling in the factory
-
Shorter transport distances for incoming deliveries
-
100% climate-compensated outgoing deliveries
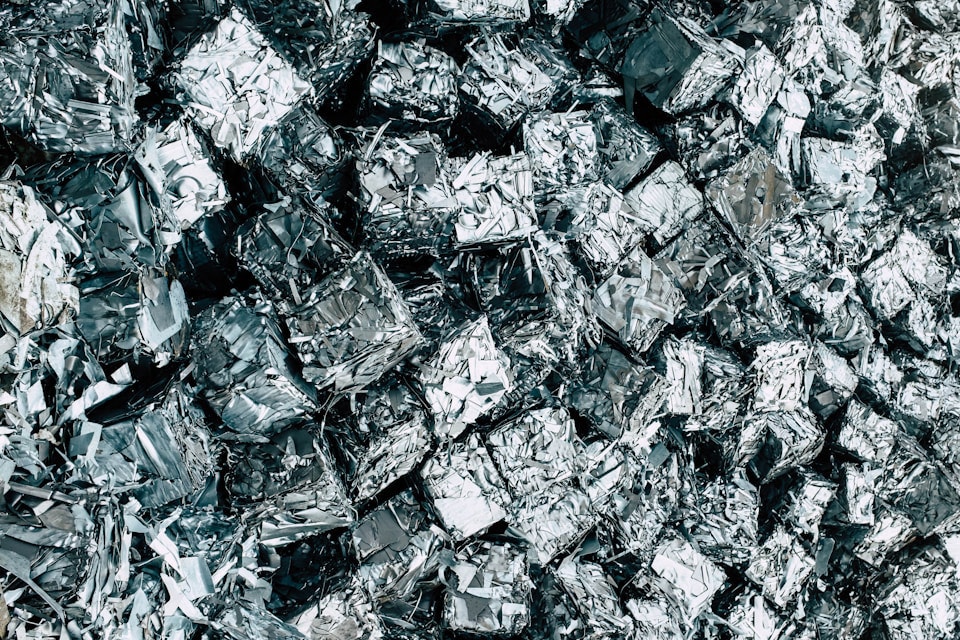
Our efforts for social sustainability
Fighting world hunger
There are significant imbalances in the global food supply chains: approximately 735 million people live in hunger, while over 1.9 billion people suffer from overweight or obesity. We are committed to fighting world hunger by actively supporting the UN World Food Programme and its mission to provide food assistance to those in need.
Learn more about the World Food Programme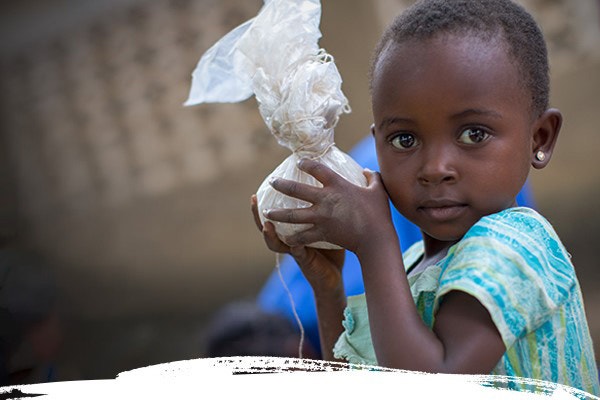
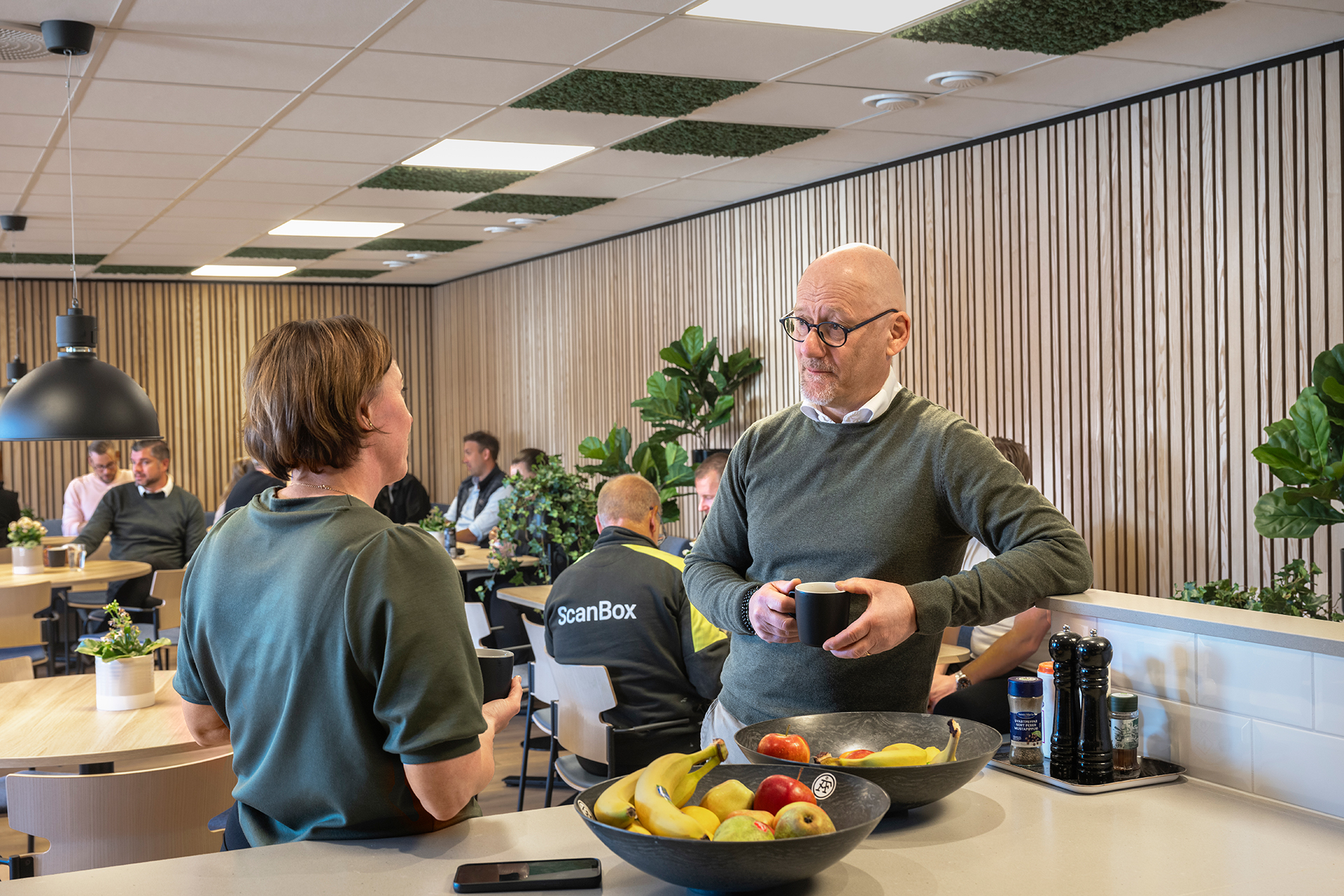
A safe and inclusive work environment
For our employees, we foster a safe and inclusive work environment by living according to our values, adhering to collective agreements, and showing respect for every individual. This ensures that all employees feel valued and appreciated in their roles.
Contributes to better working conditions
In the global commercial kitchen industry, where working conditions are often demanding and stressful, our food logistics solutions contribute to improved working conditions. By creating more balanced and efficient workflows, we support both social and economic sustainability in the industry.
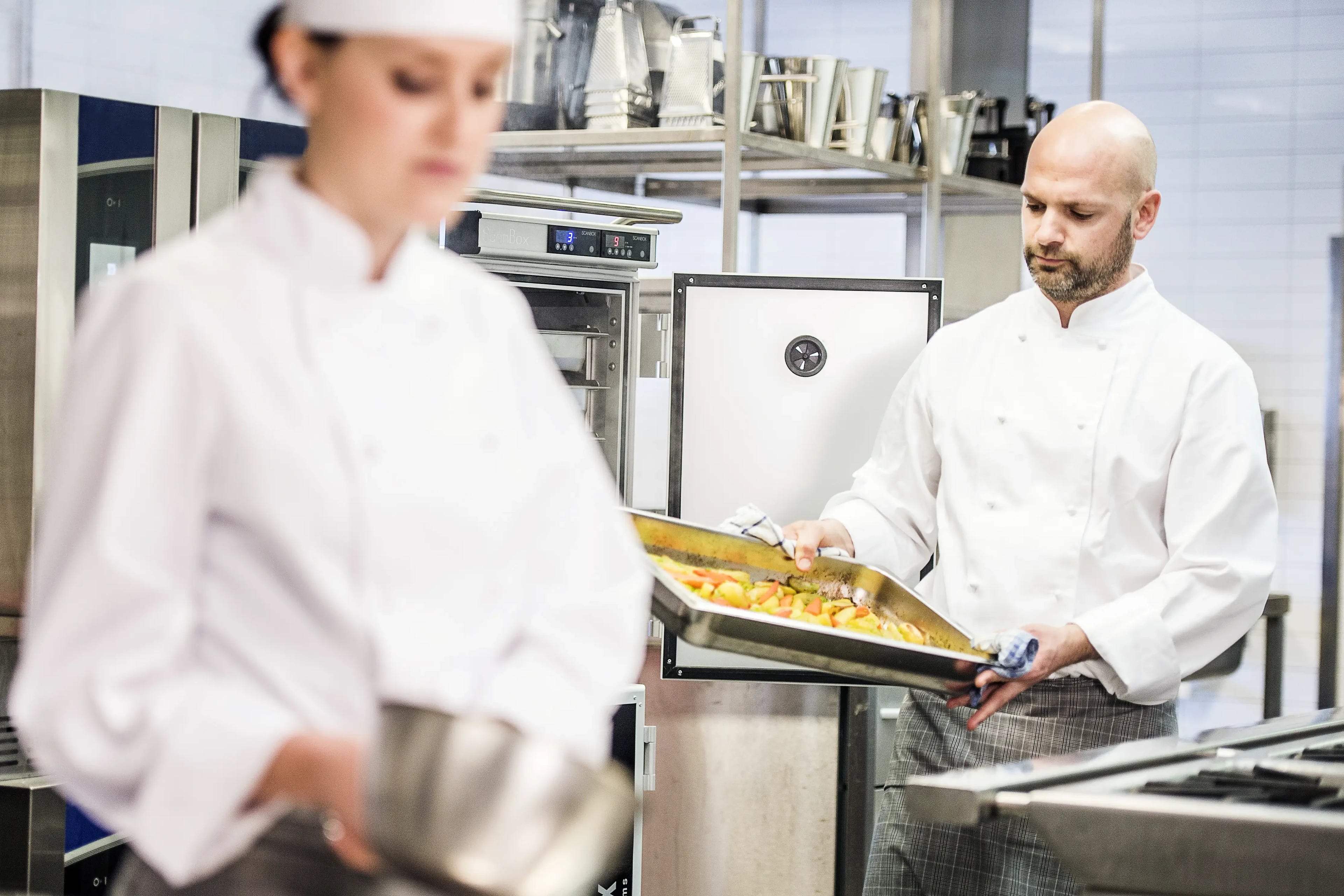
Our efforts for economic sustainability
Profitability in the global commercial kitchen industry
The global commercial kitchen industry employs over 100 million people and ensures that millions have access to nutritious food every day. Despite this, many industry players face significant challenges with profitability. A considerable portion of operations is unprofitable or inefficient, hindering their ability to provide good working environments and high-quality meal experiences.
Food logistics solutions for sustainable growth
Through our innovative food logistics solutions, we help companies in the professional kitchen industry optimize their operations. This leads to increased efficiency, improved working conditions, and better financial results. Our solutions create a foundation for sustainable operations that support a future where humanity can live sustainably while ensuring economic stability and growth in the industry.
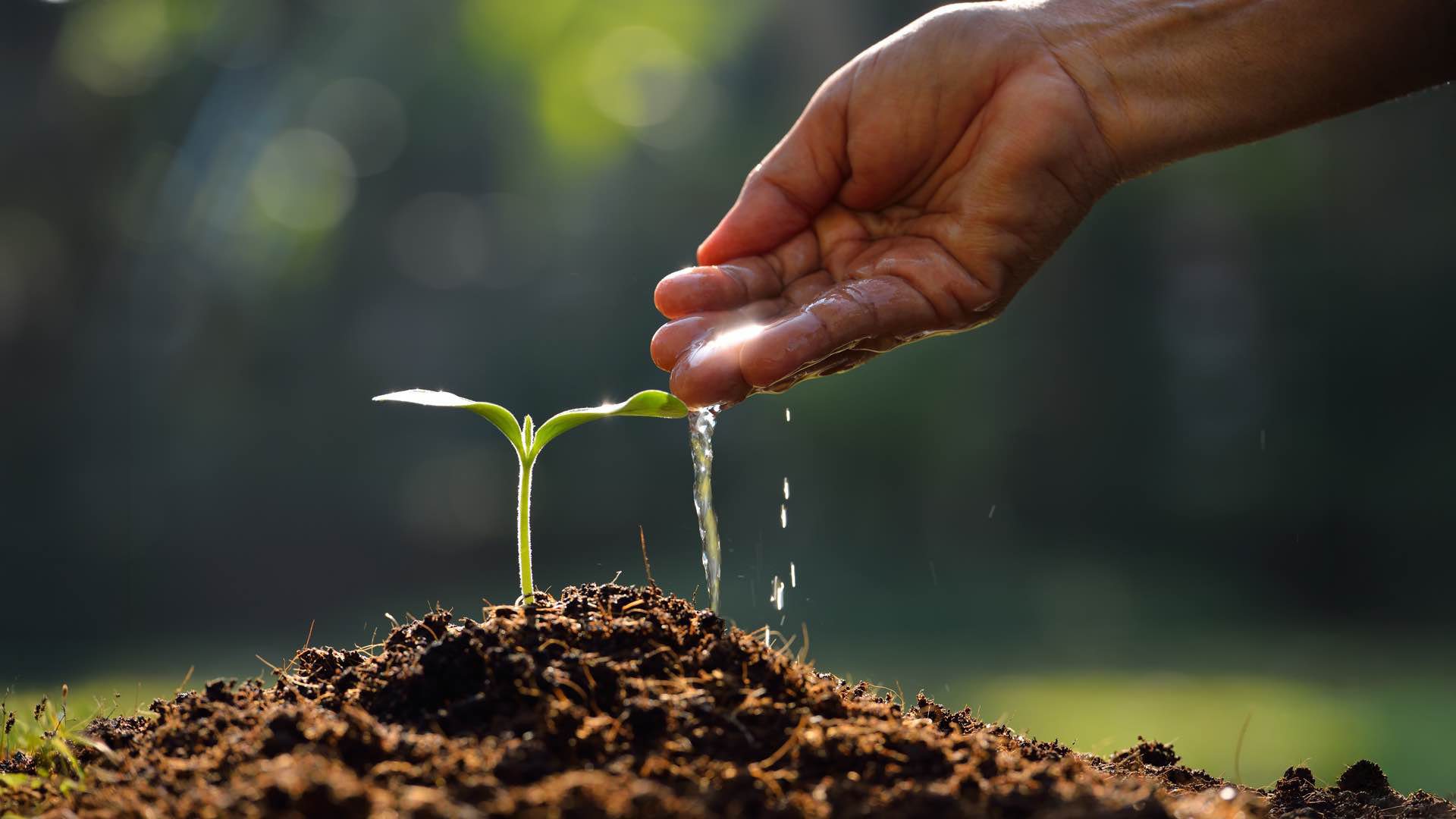
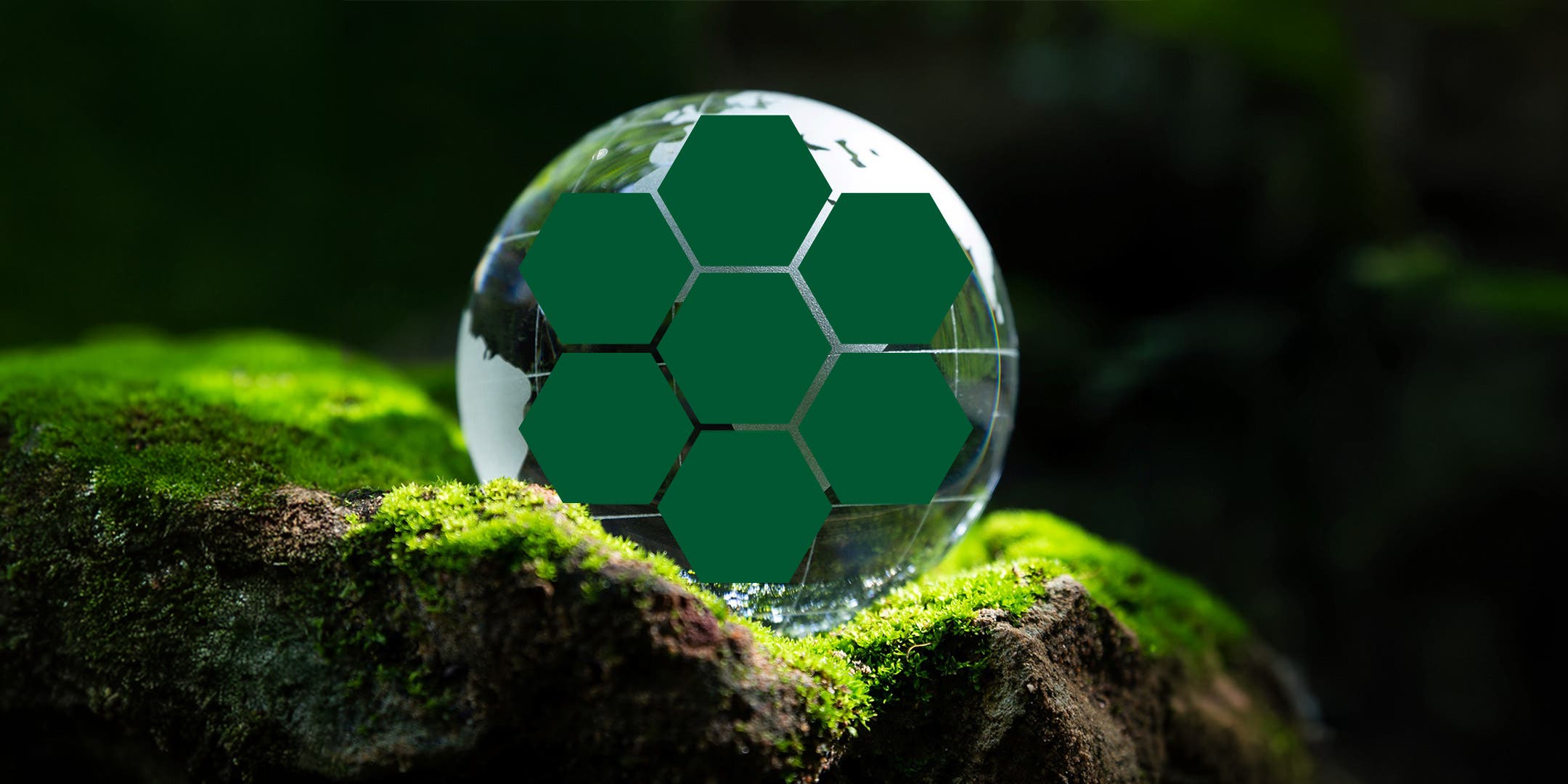
Welcome to the World of ScanBox
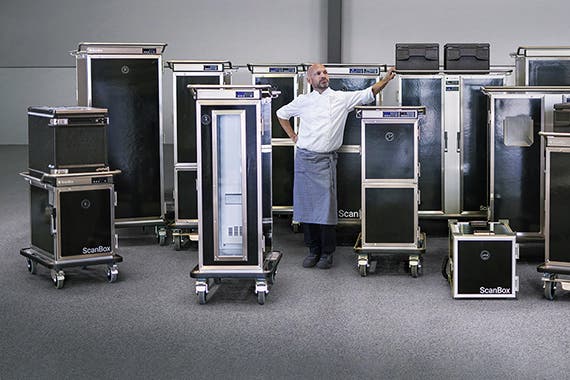
Explore our products
Discover our wide range of products designed to meet the needs of various commercial kitchens